Recognizing the Basics and Applications of Plastic Extrusion in Modern Production
In the realm of modern production, the technique of plastic extrusion plays an important function. Deciphering the fundamentals of this procedure exposes the true versatility and possibility of plastic extrusion.
The Basics of Plastic Extrusion Process
While it may show up complex, the basics of the plastic extrusion procedure are based on fairly straightforward concepts. It is a manufacturing procedure where plastic is melted and after that formed into a constant account via a die. The plastic extrusion process is thoroughly used in different industries due to its cost-effectiveness, adaptability, and performance.
Various Sorts Of Plastic Extrusion Techniques
Building upon the basic understanding of the plastic extrusion procedure, it is necessary to explore the various techniques included in this production method. The two primary methods are profile extrusion and sheet extrusion. In account extrusion, plastic is melted and formed right into a continual account, commonly used to produce pipelines, poles, rails, and home window frameworks. On the other hand, sheet extrusion creates large, level sheets of plastic, which are generally more refined into products such as food product packaging, shower drapes, and car parts. Each method requires specialized machinery and precise control over temperature level and stress to make sure the plastic keeps its shape during air conditioning. Understanding these methods is essential to utilizing plastic extrusion effectively in modern-day manufacturing.

The Duty of Plastic Extrusion in the Automotive Market
An overwhelming bulk of parts in modern cars are products of the plastic extrusion procedure. This process has revolutionized the automotive sector, changing it right into an extra efficient, affordable, and flexible manufacturing field. Plastic extrusion is mostly used in the manufacturing of different car elements such as bumpers, grills, door panels, and dashboard trim. The process gives an attire, constant output, making it possible for producers to create high-volume components with excellent precision and very little waste. The agility of the extruded plastic parts adds to the general decrease in vehicle weight, enhancing fuel efficiency. Moreover, the longevity and resistance of these components to warm, chilly, and impact enhance the longevity of automobiles. Therefore, plastic extrusion plays an essential function in auto production.
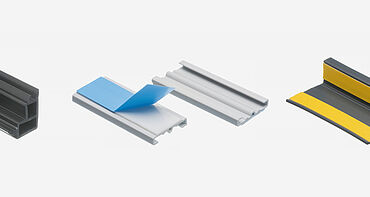
Applications of Plastic Extrusion in Durable Goods Production
Beyond its substantial effect on the automobile sector, plastic extrusion proves similarly reliable in the world of customer items manufacturing. content The versatility of plastic extrusion permits suppliers to create and create complicated shapes and sizes with high accuracy and effectiveness. The flexibility, adaptability, and cost-effectiveness of plastic extrusion make it a favored choice for numerous consumer products manufacturers, adding dramatically to the sector's development and technology.
Ecological Effect and Sustainability in Plastic Extrusion
The prevalent use plastic extrusion in producing welcomes scrutiny of its environmental ramifications. As a process that regularly utilizes non-biodegradable products, the environmental effect can be considerable. Energy intake, waste manufacturing, and carbon discharges are my latest blog post all issues. Nonetheless, sector advancements are enhancing sustainability. Reliable equipment minimizes power use, while waste management systems recycle scrap plastic, lowering raw material needs. In addition, the development of eco-friendly plastics uses an extra eco-friendly choice. Regardless of these renovations, better advancement is needed to minimize the ecological footprint of plastic extrusion. As society leans towards sustainability, producers should adapt to remain practical, stressing the relevance of continuous research and improvement in this field.
Final thought
In final thought, plastic extrusion plays a vital function in modern production, especially in the vehicle and consumer products sectors. Its flexibility enables the manufacturing of a vast array of parts with high precision. Additionally, its possibility for why not try these out recycling and advancement of biodegradable products provides an appealing method in the direction of sustainable methods, therefore addressing ecological problems. Recognizing the fundamentals of this process is crucial to optimizing its applications and benefits.

The plastic extrusion process is extensively used in different markets due to its versatility, cost-effectiveness, and performance.
Building upon the fundamental understanding of the plastic extrusion process, it is needed to explore the different techniques entailed in this production technique. plastic extrusion. In contrast, sheet extrusion creates big, level sheets of plastic, which are commonly additional processed into items such as food packaging, shower drapes, and car parts.A frustrating majority of parts in modern-day cars are products of the plastic extrusion process